
PROCESS
Lean Six Sigma training: Yellow, green and black belt
The Lean Six Sigma methodology is a globally recognised approach to process improvement, waste reduction, and operational excellence.
Enhance business performance
Develop data-driven decision-making
Build leadership capability
Achieve industry-standard qualifications
Who should attend?
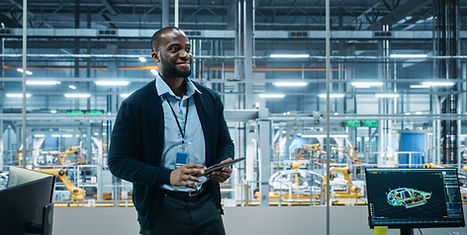
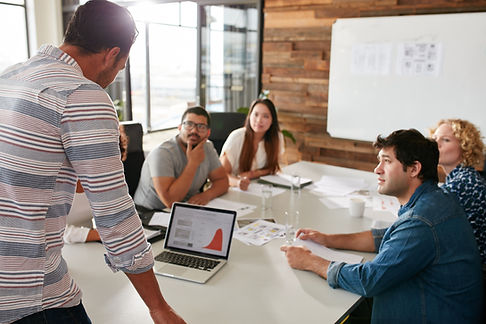
These qualifications are ideal for
01.
Lean Six Sigma Yellow Belt – All employees, especially those new to Lean Six Sigma. Provides a foundational understanding to support and engage in problem-solving activities.
02.
Lean Six Sigma Green Belt – Team leaders, supervisors, and managers actively involved in identifying, analysing, and implementing process improvements.
03.
Lean Six Sigma Black Belt – Senior managers, Lean practitioners, and continuous improvement (CI) leaders seeking to coach teams, drive cultural change, and lead strategic Lean Six Sigma transformations.
Qualification structure
The Lean Six Sigma methodology is a globally recognised approach to process improvement, waste reduction, and operational excellence.
01
Lean Six Sigma
Yellow Belt
The Lean Six Sigma Yellow Belt course provides participants with a foundational understanding of Lean Six Sigma principles and the importance of structured problem-solving.
This programme introduces the core methodologies of Lean and Six Sigma, equipping individuals with the knowledge to support CI initiatives.
Course structure
This one-day course provides a mix of theory, discussion, and practical exercises.
-
Fundamentals of Lean Six Sigma
-
Understanding Lean and Six Sigma methodologies.
-
Exploring the importance of reducing waste and variation.
-
-
Problem-solving and process improvement
-
Introduction to the DMAIC framework.
-
Hands-on exercises using basic Lean and Six Sigma tools.
-
-
Role of a Yellow Belt in CI initiatives
-
Understanding how Yellow Belts contribute to team-based problem-solving.
-
Applying visual management and data-driven decision-making.
-
Certification requirements
-
Completion of the one-day training.
-
Demonstration of understanding through engagement in practical exercises.
02
Lean Six Sigma
Green Belt
The Lean Six Sigma Green Belt equips professionals with the tools and knowledge to lead improvement projects, enhance efficiency, and reduce variation.
Positioned between Yellow Belt (introductory level) and Black Belt (expert level), this training builds practical CI capability.
Course structure
This six-day programme is structured into three two-day sessions, allowing for practical application between training blocks.
-
Define phase
-
Introduction to Lean, Six Sigma, waste, and variation.
-
Project selection and defining the problem statement.
-
-
Measure phase
-
Understanding current performance and process variation.
-
Using data collection and visualisation techniques.
-
-
Analyse phase
-
Identifying and validating true root causes.
-
Using data-driven analysis to drive decision-making.
-
-
Improve phase
-
Selecting, testing, and optimising solutions to eliminate root causes.
-
Using Lean methods to enhance efficiency.
-
-
Control phase
-
Embedding sustaining measures to monitor improvements.
-
Implementing Leader Standard Work and visual controls.
-
Certification requirements
-
Completion of the six-day training.
-
Successful application of DMAIC methodologies in a real-world project.
03
Lean Six Sigma
Black Belt
The Lean Six Sigma Black Belt is designed for experienced practitioners leading complex improvement initiatives and driving strategic Lean transformations.
This programme equips participants with the expertise to mentor teams, optimise processes, and create data-driven solutions.
Course structure
This advanced programme is delivered over ten days, typically structured into five two-day sessions.
-
Advanced define and measure phases
-
Refining project selection and stakeholder engagement.
-
Mastering data collection and advanced statistical analysis.
-
-
In-depth analyse phase
-
Using regression analysis, hypothesis testing, and advanced root cause techniques.
-
Applying failure mode and effects analysis (FMEA).
-
-
Leading high-impact improvement initiatives
-
Developing and implementing sustainable Lean Six Sigma solutions.
-
Managing risk and ensuring solutions deliver long-term results.
-
-
Control and sustainment strategies
-
Embedding performance measurement systems and control plans.
-
Coaching and mentoring Green Belts and project teams.
-
Certification requirements
-
Completion of the ten-day training.
-
Demonstration of expertise through the completion of a high-impact project.
-
Successful assessment of leadership and coaching competencies.
Looking for a public workshop?
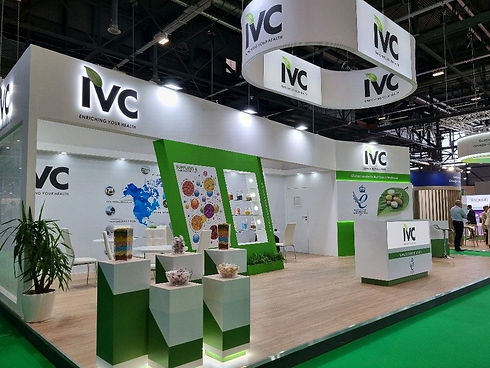