
DISCOVERY
Productivity assessment
The productivity assessment provides an objective evaluation of your site’s operational performance, identifying gaps, waste, and improvement opportunities.
Boost operational performance
Drive productivity gains
Strengthen culture and accountability
Focus on what matters
Unlocking productivity potential across your plant
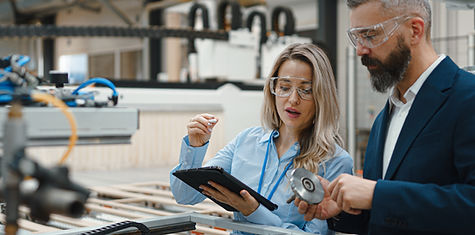
The productivity assessment provides an objective evaluation of your site’s operational performance, identifying gaps, waste, and improvement opportunities.
This comprehensive assessment helps senior leaders understand their current performance against best practice and develop a prioritised roadmap to drive sustainable productivity gains.
Our Approach
Our assessment offers a holistic evaluation of productivity across your manufacturing site or business unit.
We deploy two experienced practitioners who apply a fact-based, objective approach using data analysis, interviews, group discussions, and Gemba observations.
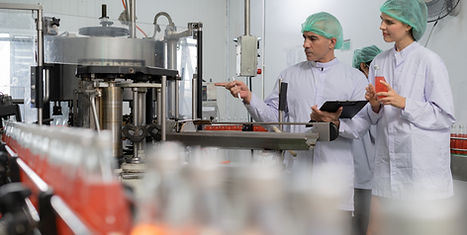

We review performance across multiple areas, including:
-
Safety and quality – Assessing risk management and product consistency.
-
Productivity and waste – Identifying inefficiencies, downtime, and lost output.
-
Flow and inventory – Evaluating production flow and stock management.
-
People capability and culture – Reviewing skills, engagement, and morale.
-
Processes and systems – Assessing work standards, procedures, and adherence.
-
Leadership and communication – Evaluating management behaviours, accountability, and performance reviews.
-
Problem-solving and metrics – Understanding how issues are identified, resolved, and tracked.
The three-phase process
The productivity assessment provides an objective evaluation of your site’s operational performance, identifying gaps, waste, and improvement opportunities.
01
Preparation
-
Collecting relevant data and performance metrics.
-
Understanding your strategic goals and current challenges.
-
Planning on-site assessment activities and stakeholder engagement
02
On-site assessment
-
Conducting 1.5-2 days of plant observation, interviews, and group sessions.
-
Reviewing processes, performance measures, and leadership practices.
-
Identifying waste, gaps, and strengths across the plant.
03
Reporting and follow-up
-
Delivering a detailed assessment report outlining strengths, gaps, and priority improvement areas.
-
Providing quantitative scoring an
comparison to best practices. -
Presenting clear recommendations and a practical roadmap to achieve rapid and sustainable productivity improvements.
