
Manufacturing glossary of terms
Unlock the secrets of manufacturing with our glossary of terms developed over 40 years by George Donaldson, Shingo Prize recipient! Take a deep dive into industry jargon. Don't wait! Master your industry knowledge NOW!
The story of how this glossary was created and has evolved, in the words of author George Donaldson.
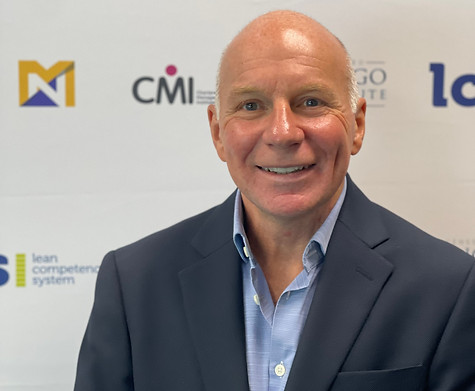
This glossary’s roots began in 2010 when I worked with Newsprinters Eurocentral Ltd. I noticed less emphasis on the practice and principles of Organisational Excellence in manufacturing and more on the language used to describe them.
Of course, people then became concerned about learning vast amounts of new words rather than paying attention to what they meant. Many terms also came about in the 1950s, and their original definitions weren’t applicable today. What we needed was a single reference point – a glossary. So, that’s what I created.
As I moved away from Newsprinters Eurocentral Ltd and worked with other businesses, I expanded the glossary to include all models and other tools and techniques. I was teaching courses in Continuous Improvement and realised manufacturing needed to be demystified; students were often overwhelmed with various acronyms.
Then, as manufacturing became about more than just improvement – and about leadership, management, and psychology too – the glossary grew once more. It now includes theories from the likes of Maslow, Herzberg, and McGregor, and even modern theorists such as Sinek. I’ve also included the GROW model to reflect manufacturing’s focus on developing people through coaching and mentoring.
Manufacturing is much more holistic today. And this glossary echoes that. Sitting at over 300 definitions, you’ll be able to find any term you need to achieve Organisational Excellence in the modern world.
Good luck on your journey.
George Donaldson
Term:
3 Insights for Organisational Excellence
As part of the Shingo Institute research, they identified three key insights of organisational excellence:
Insight 1: ideal results require ideal behaviours. Ideal results are any outcomes that are both sustainable and excellent. Ideal behaviours are any actions that create those outcomes that are both sustainable and excellent.
Insight 2: purpose and systems drive behaviour. This is based on the understanding that firstly, when people understand the why behind what they are doing, they do a better job and secondly, that systems drive or influence how we behave.
Insight 3: principles are self-evident, govern the consequences and inform or determine the ideal behaviour.
The late Stephen Covey, author of The 7 Habits of Highly Effective People, stated that, “While values drive behaviours, principles govern the consequences.”
Term:
3 Standard Deviations
3 Standard Deviations, or 3 Sigma, basically means that i3 standard deviations from the mean will account for 99.7 per cent of the data.
Term:
3M
The lean 3M incorporates three Japanese words: Muda, Mura and Muri:
1. Mura: means waste and covers the seven or eight wastes
2. Mura: means unevenness and refers to the uneven flow or distribution of activities (work), machines and processes
3. Muri: means overburden and refers to stress on people and machines (See Muda − Mura − Muri − Seven wastes or eight wastes)
Term:
3P
The lean 3Ps stands for People, Purpose and Process:
1. People: satisfaction of both internal and external customers
2. Purpose: everyone in the organisation is aligned with the strategy and clearly understands how their contribution helps achieve the business goals
3. Process: continuous improvement of all the operations and activities is at the heart of continuous improvement
Some organisations have adapted the 3Ps to be associated with three main safety factors:
1. People: protecting our people is our number one priority (safety)
2. Product: protecting our product and customer (hygiene)
3. Planet: protecting inside and outside the business (environment)
Term:
5 Whys
5 Whys is a technique used to determine the root cause of a problem.
By asking why repeatedly, you can generally determine the root cause to most problems or issues and in doing so, normally come up with the best solution.
Term:
5M
The 5Ms are five categories starting with ‘M’ commonly used when using a cause-and-effect diagram:
Man, Method, Machine, Material, Mother Nature.
Term:
5S
5S is the most fundamental process for continuous improvement (CI) and total productive manufacturing (TPM).
It is based on five Japanese words starting with the letter S. The English translation is:
Sort - only keep what is required.
Set in order - a place for everything and everything in its place.
Shine - asset care inside and out.
Standardise - set standards to maintain first three ‘S’s.
Sustain - audit, audit, audit and drive continually to improve the first 4 ‘S’s.
The basic rule for 5S is that you should be able to find whatever you are looking for within 30 seconds.
Term:
5W–2H
5W–2H is a process for clearly defining an issue, problem or situation:
Who - who was involved? - who reported it?
What - what was the issue? - what happened?
Where - where did it occur? - specific location
When - when did it occur? - actual day, date, time, shift.
Why - why is this important? - is this a priority?
How - how did it occur? - how was it noticed?
How much - how much did it cost? - how frequently has it occurred?
Term:
6 Big Losses
The 6 Big Losses are exposed through overall equipment effectiveness (OEE) and the factors of availability, performance and quality.
Each factor generates two big losses, which when identified and resolved, will improve OEE:
Availability losses
Breakdowns.
Set-up and adjustments.
Performance losses
Small stops.
Reduced speed.
Quality losses
Start-up rejects.
Production rejects.
Term:
6 Sigma
6 Sigma is a business management strategy that was developed by Motorola.
The methodology behind the 6 Sigma strategy is to ensure that the customer comes first.
Its aim is to deliver highest quality at the lowest possible cost, eliminating or reducing all variation, focusing on 7 wastes and the business’ hidden factories.
6 Sigma also uses DMAIC and SPC as its base process tools.
Term:
68-95-99.7 Rule
The 68-95-99.7 Rule, also known as the empirical rule, is a statistical rule used as a reminder of the percentages of distribution that fall within one, two and three standard deviations.
Term:
6P Model
The 6P Model is designed as a holistic people-centric approach. Therefore, for an organisation and its people to achieve their full potential, all six disciplines must be treated systemically as they are interdependent and interrelated and cannot be viewed in isolation from each other.
People: encompasses everyone within the organisation, from board room to shop floor.
Partners: involves customers, suppliers and supply chains, vendors, contract or agency employees, stakeholders, and community.
Purpose: entails the organisation’s mission, vision, principles, values, strategies and alignment.
Plan: is the development, alignment, deployment and execution of the organisation’s strategies and activities.
Process: covers all the systems, processes and practices that produce the products and services and support the organisation.
Performance: consists of the organisational measures and results that support the decision-making, problem-solving, continuous improvements, sustainability and growth of the organisation and its partners.
Term:
7 (Basic) Quality Tools
The 7 (Basic) Quality Tools are a set of tools that were introduced by Kaoru Ishikawa (who was influenced by W. Edwards Deming). Ishikawa argued that 95% of problems can be resolved by using these tools:
Process map.
Cause and effect diagram.
Check sheet.
Histogram.
Pareto chart.
Scatter diagram.
Control chart.
Term:
7 Wastes or 8 Wastes
7 Wastes are categorised under: transportation, resources, inventory, motion, waiting, over-production, over-processing and defects.
The eighth waste is people (talent and potential).
It is the aim of TPM, Lean manufacturing and CI to identify and eliminate these wastes as they do not add value to the business and the customer is not paying for them.
Term:
7S McKinsey Management Model
The 7S McKinsey Management Model was developed by Tom Peters and Robert Waterman (authors of In Search of Excellence) while they were consultants at McKinsey.
The model is designed to aid business strategic development, deployment, and alignment.
The 7Ss are structure, strategy, systems, skills, style, staff, and shared values.