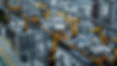
PURPOSE
Value stream mapping
Value stream mapping (VSM) is a powerful tool that gives leaders an end-to-end perspective of a product family’s flow.
End-to-end visibility
Identify waste and bottlenecks
Drive strategic alignment
Support continuous improvement
A strategic tool for alignment and improvement

Value stream mapping (VSM) is a powerful tool that gives leaders an end-to-end perspective of a product family’s flow.
It enables teams to align on the current state, identify inefficiencies, and create a roadmap for transformation. We have extensive experience in facilitating VSM workshops and transferring knowledge and capability in these important skills.
Our Approach
We engage leaders and subject matter experts in selecting and analysing a strategically important value stream to visualise a future-state VSM and co-create a roadmap for transformation.


Before the workshop stages, we support the planning and preparation activities where you will define or select a value stream, form a VSM team, develop a VSM charter, and begin data collection.
We then facilitate collaborative workshops that bring together leadership, subject matter experts, and key stakeholders to identify waste and improvement opportunities – simultaneously transferring knowledge and capability throughout. By the end, they will have aligned on an actionable transformation plan for the value stream.
The three-phase process
Value stream mapping (VSM) is a powerful tool that gives leaders an end-to-end perspective of a product family’s flow.
01
Mapping the current state
-
Visualising the entire value stream, from order intake to product delivery.
-
Examining both information flow (customer orders, scheduling, and planning) and material flow (supplier inputs, manufacturing, assembly, and shipping).
-
Identifying waste, bottlenecks, inventory levels, and key performance metrics.
02
Defining the future state
-
Using Lean principles and the ‘8 wastes’ framework to design an improved value stream.
-
Developing multiple future states – a long-term aspirational vision and a short-term, achievable target condition.
-
Prioritising improvements based on impact and feasibility.
03
Building the transformation plan
-
Creating a structured roadmap with timelines, resources, and ownership.
-
Ensuring leadership commitment through clear accountability and governance.
-
Supporting knowledge transfer and capability-building throughout the process.
