Pull Systems In Lean: Demand-Driven Processes
- Mark Leeson
- Nov 7, 2023
- 3 min read
Updated: Nov 20, 2023
Lean manufacturing embraces efficiency and a customer-centric approach. And at the heart of Lean is the concept of pull systems to prompt demand-driven Organisational Excellence. Within pull systems, supply chains find their rhythm and inventory levels hit the right note – meaning improved customer satisfaction.
This article investigates pull systems, their benefits over traditional push systems, and how to implement this demand-driven process in business operations.
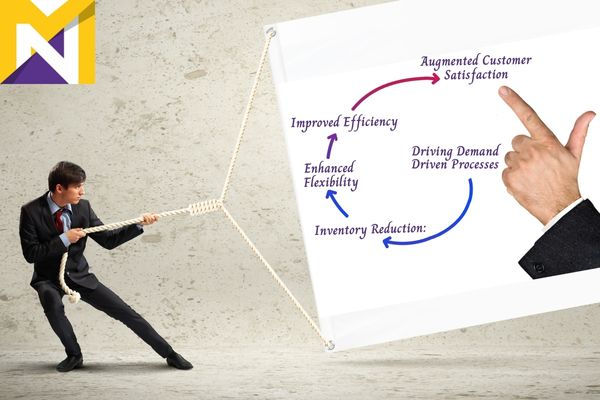
Introduction to pull systems
Pull systems represent an approach where the production responds to real customer demand, contrasting with traditional forecast-driven push systems. The essence of pull systems lies in their reactionary nature, where processes are triggered by actual orders, creating a Lean supply chain that moves in time with market demand.
In a pull system, every segment of the operational flow reflects real-time demand, ensuring that resources are used efficiently, and inventory is meticulously managed.
Benefits of a pull over push system
Inventory reduction: Pull systems are synonymous with just-in-time inventory, where resources are procured and products manufactured in direct response to demand, significantly reducing the need for storage space and minimising holding costs.
Enhanced flexibility: The ability to respond to actual demand enables a business to flex its operational muscles precisely where and when needed. This leads to better adaptability to market changes, ensuring a steadier sail through market variability.
Improved efficiency: Pull systems promote a culture of Continuous Improvement by illuminating bottlenecks and waste. Aligning operations to real demand streamlines processes.
Augmented customer satisfaction: Operating in a demand-driven framework ensures that customers receive what they want when they want it. This elevated level of service enhances customer satisfaction and enduring relationships.

Implementing pull systems in business
Implementing pull systems necessitates a blend of strategic insight, operational tweaks, and an unyielding commitment to Lean principles. Here are actionable steps:
Look into historical sales data, engage with customers, and analyse market trends to gain a nuanced understanding of demand patterns.
Immerse your organisation in Lean thinking to promote a culture of Continuous Improvement and prioritise value delivery in every process.
Implement Kanban systems to visualise workflows, manage work in progress, and ensure a seamless flow of value from inception to delivery.
Cultivate a collaborative environment where teams are engaged, educated on the pull system mechanics, and empowered to take action.
Continually monitor key performance indicators and identify areas of improvement to drive Organisational Excellence.
An example application of pull systems in lean
A medium-sized manufacturer of automotive parts faced challenges with overproduction, high inventory levels, and an inability to adapt quickly to market changes. Under the old push system, production schedules were based on forecasted demand, which often led to discrepancies between manufactured goods and actual market needs.
Transition to a pull system
The company began by understanding and conducting a thorough analysis of historical sales data, market trends, and customer feedback to understand demand patterns better.
A comprehensive training programme was instituted to educate employees about lean principles, the mechanics, and the benefits of a pull system.
They chose to implement a Kanban system, a popular pull system methodology. They set up Kanban boards to visualise work processes and created a pull signal system to initiate production based on actual demand.
They engaged suppliers early to ensure they were aligned with the new demand-driven approach. They worked closely with suppliers to set up Just-In-Time (JIT) delivery schedules, reducing lead times and minimising stockouts.
Initially, a pilot test was run in a specific department to gauge the effectiveness and potential challenges of the new system. The success seen in the pilot stage provided the confidence to roll out the pull system across the entire organisation.
The company leveraged modern technology by implementing Demand-Driven Material Requirements Planning (DDMRP) systems to optimise operations, ensuring real-time visibility and better decision-making.
Outcomes and reflection
After implementing the pull system, the manufacturing company witnessed a significant reduction in inventory levels, enhanced process efficiency, and a better alignment of production with actual market demand. Moreover, they saw an improvement in supplier relationships, a reduction in lead times, and an overall increase in customer satisfaction due to better delivery rates.
The company’s journey highlights the intrinsic value of adopting a pull system within a lean supply chain framework. By making a structured transition to a pull system, they not only streamlined its operations but also fostered a culture of Continuous Improvement, better positioning the company in a competitive market. Through a methodical approach to implementing a pull system, they successfully transitioned to a demand-driven operational model, embracing Lean principles.
Pull systems in Lean
Adopting pull systems enhances efficiency and responsiveness and places the customer at the centre of business operations. As organisations strive towards a demand-driven approach, pull systems in Lean boost Organisational Excellence and customer relationships.
If you would like to learn more, please contact us:
Phone: 0161 533 1617
Email: [email protected]